Penetrating Pulse Technology:
A safe, economical, non-contact, non-invasive, “through the wall” digital technology for accurate level measurement
by Leif Lindvall, HiTECH Technologies, Inc., Yardley, Pa.
For years, process industries have been seeking reliable techniques for measuring or detecting liquid levels. This is now possible with digital penetrating pulse technology. Its advantages include:
- No physical contact with the liquid because the acoustic energy transducers mount outside of the vessel
- No possibility of leakage or contamination
- Measurement is independent of pressure and the presence of vapor and foam on the surface of the liquid
- Measurement is not affected by toxic, aggressive or corrosive liquids
- Easily retrofits to existing vessels without welding
- No pressure vessel re-certification required
Principle of Operation
The measurement principle is simple and easy to understand. A special acoustic energy transducer, mounted in direct contact with the vessel’s outside wall, emits a short pulse of acoustic energy. The pulse penetrates the vessel wall and any tank lining and travels through the liquid. Depending on the operating mode, the pulse is either reflected back to the transducer or detected by another transducer. The transit time, together with other application parameters, reveals the actual level in the vessel. While the same technique can be applied to both continuous level measurement and point-level detection, implementation is somewhat different in each case.
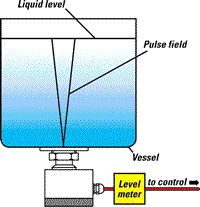
Continuous Level Measurement
The transducer is mounted in direct contact with the bottom of the vessel (see Figure 1). The liquid/air or liquid/liquid interface reflects the signal back to the device. The measured level in the vessel is a function of the pulse’s transit time and other variables, such as wall thickness, vessel shape, material characteristics and temperature. A sophisticated algorithm built into the instrument processes the variables and determines the liquid level.
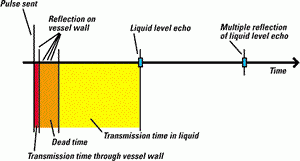
Figure 2 shows the pulse position as a function of time. Part of the transmitted pulse produces multiple reflections from the vessel’s inside wall. The transducer detects these interfering reflections as early echoes and eliminates them with a dead time, during which returning signals are ignored. This means that levels cannot be measured down to zero depth.
A tolerance band is placed around the mean transmission time and only measured values inside the expected range are included in the calculation of further values. The transmission time is converted to depth on the basis of the speed of sound. Because sonic velocity depends on the kind of liquid and its concentration and temperature, a correction factor can be programmed. Compensation also may be required if the operating temperature changes substantially.
Temperature Compensation
If the vessel always contains the same liquid, transducers with
integral temperature sensors can eliminate the effect of temperature- induced changes in the speed of sound. However, inaccurate level measurements are still possible in a stratified liquid with different temperatures in each layer.
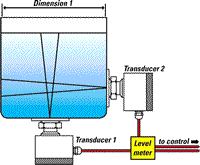
Compensation with Reference Measurement
If a vessel is filled with various liquids, the concentration or chemical composition changes and the acoustic transmission characteristics may change also. In these applications, a second measuring channel of a dual channel device monitors the acoustic characteristics of the liquid as a reference measurement. This is used with the first channel to calculate the actual level. The reference signal must travel through the vessel horizontally (see Figure 3).
Unit Conversion
Percentage level is the basis for subsequent calculations and outputs. Converting the liquid level from percentage to volume requires digitizing the vessel shape and its dimensions. These variables are programmed into the device at set-up. This results in the output being scaled in preferred volumetric units of measure, such as gallons or cubic feet.
Measurement Response Time
Instrument response time can be adjusted by programming the data update intervals. Doing so affects the measured values, the local display panel, the current outputs and the switching signals.
Point-level Detection
In point-level measurements, the pulse penetrates the vessel wall, enters and radiates through the liquid. Depending on the particular measuring mode being used, the reflected pulse may be received by the same transducer or by a separate transducer mounted on the other side of the vessel.
The controller software has a point-level algorithm with a preset threshold value. A programmable time integration function prevents intolerable jitter in the switched output. The controller supports several operating modes:
- Pulse-echo mode with one sensor
- Pulse-echo mode with two sensors
- Pulse transmission with two sensors
- Dying out pulse with one sensor
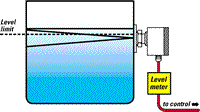
Pulse Echo Method
In the pulse-echo method with lateral transducer attachment, the transducer is attached to the vessel at the height of the level switch point (see Figure 4). If the vessel is filled with liquid to the specified level, the transducer receives a reflected echo. If no liquid is present at this level, there is no echo. The presence or absence of echo at the expected point is evaluated by the link-up with the time window (gate) and the instrument outputs the corresponding signal.
Application requirements include:
- Pipes or vessels with parallel walls
- A minimum path length of eight in. for metal or glass and two in. for plastic
- A maximum path length of 66 ft
- No agitator or internal fittings at the elevation of the level detection point
- Pure (low-absorbing) liquids, free of bubbles and suspended solids
This system can monitor the level in ice silos of flake ice makers in refrigeration systems. It can detect chemical reactions, such as crystallization or polymerization. It can detect pigs in pipelines.
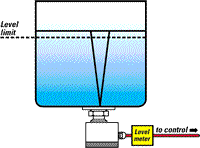
Pulse-echo Method with Vertical Sensor Attachment
The transducer directs the pulse upward to within two or three degrees of vertical. The surface of the liquid reflects the pulse back to the sensor (see Figure 5). The gate setting sets the monitored filling level. The temperature drift of the velocity of acoustic transmission and the time needed for the pulse to return must be taken into consideration.
Applications include:
- Substitute for continuous level monitoring
- Vessels with height from approx. 2 in. to 66 ft
- No agitator or internal fittings in pulse path
- Liquids, free of bubbles and solids
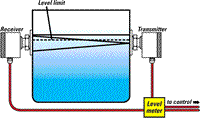
Pulse Transmission
For pulse transmission, two transducers are attached to the vessel at opposite sides (see Figure 6). One functions as the transmitter; the other as the receiver. This method requires a dual channel device.
Applications include:
- Sound-absorbing liquids laden with gas bubbles or contaminants, such as suspended solids
- Level in pipes (requires special angle adapters)
- Vessels with diameters to 66 ft
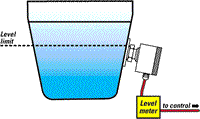
Dying Down
Dying down involves evaluating signal decay. A sensor is attached to the outside of the vessel at the same level as the liquid limit (see Figure 7). If no liquid is present at this level, the metal wall is not attenuated and it vibrates for a long time under the impact of the ultrasonic pulse. Any liquid present at this level eliminates the vibration. Applications include:
Metal vessels with a diameter of more than eight in. and wall thickness of 0.08 to 0.8 in.
Sound-absorbing liquids.
The liquid must not leave any residue on the vessel wall.
No reflecting wall or internal fittings in the vessel.
Transducers
One major breakthrough that enables penetrating pulse technology for liquid level measurement is the acoustic energy transducers. Transducer selection depends upon a number of factors including:
- Vessel geometry
- Material of construction
- The nature of the liquid
The mounting configuration and acoustic coupling between the transducer and vessel wall is critical to accurate level measurement. Therefore, certain points need to be observed when mounting a transducer. The surface at the point of attachment must be extremely flat and smooth. Paint or other surface treatments are detrimental and should be removed. Applying a special acoustic mounting compound between the transducer and vessel can compensate for some degree of surface unevenness.
Because there are numerous considerations involved in selecting the most appropriate transducer and mounting configuration, discuss your specific application in detail with a supplier trained in penetrating pulse technology.
Start-up
Older systems require an oscilloscope for installation, start-up and commissioning. Modern technology features a built-in oscilloscope function to simplify the process. Start-up requires only a notebook computer running Windows 95, 98 or 2000 (see Figure 8).
Although there are numerous factors involved in applying this technology properly, penetrating pulse technology is a desirable level measurement alternative, particularly in the biotech, chemical, food and beverage, liquefied gas, oil pipeline and pharmaceutical industries.
For example, a major chemical manufacturer is replacing its nuclear and radar level systems with the penetrating pulse technology level systems to completely eliminate the possibility of leakage and the bureaucratic nightmares of licensing and testing.
Digital penetrating pulse technology is especially suitable for vessels containing liquefied flammable gases because it can be installed without welding or drilling. The devices can be attached to the vessels with a special adhesive or stainless steel straps.